3D Printing – Audio plastic shell - QSYrapid
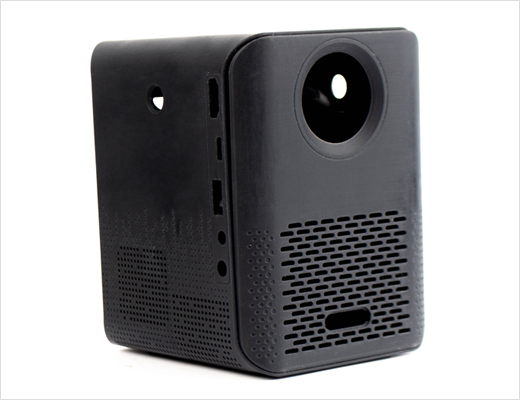
Case introduction
Discover how 3D printing is revolutionizing the creation of audio plastic shells. Learn how designers use 3D models to verify designs for thermoplastic moldings. Visit QSYrapid for more on online 3D printing services.Nowadays, 3D models and verification models are often made using 3D printing technology, which can provide more efficient and accurate manufacturing solutions.
This case is a prototype of the appearance of a speaker printed using the QSYrapid SLA 3D printing process. The material used is photosensitive resin. After the printing is completed, it undergoes basic manual polishing, then measurement and quality inspection, and then oiling, and final assembly. as shown in the diagram.
We make plastic product shells for our customers. When making product appearance models, we will select different plastic materials based on the usage of the customer's shell model. Different materials also have different physical properties. For example, if the customer is doing ordinary appearance structure verification, then the photosensitive resin is used. The advantage of photosensitive resin is that it is relatively smooth and cheap, but the disadvantage is that it is relatively brittle. Of course, you can also choose imported photosensitive resin materials to make the structure and appearance of the prototype shell, and you will get a product with better toughness.
Nowadays, the prototype production process is becoming more and more efficient and fast. The characteristics of the prototype or the product itself are that the more components there are, the longer the supply chain and product line will be, and the more time and cost will be required for assembly and transportation. The integrated forming of 3D printing eliminates the need for reassembly, thus shortening the supply chain and saving costs on labor and transportation. The 3D printing process makes the production of prototype parts more efficient and faster.
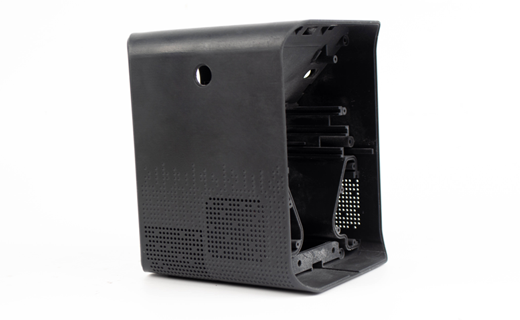
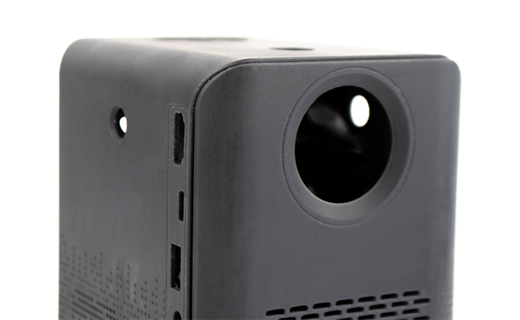