Differences in 3D Printed Materials
Introduction
3D printing, also known as additive manufacturing, has revolutionized product design and development. By building objects layer-by-layer based on digital models, 3D printing enables the creation of complex geometries and customized products. A key consideration in any 3D printing application is the selection of the appropriate material. Two popular materials for consumer and industrial printing are thermoplastic polyurethane (TPU) and polyurethane (PU). This article explores the key properties, applications, and comparative advantages of TPU and PU in 3D printing.
Overview of 3D Printing Materials
The range of materials compatible with 3D printing has expanded enormously over the past decade. Polymers such as ABS, PLA, PETG, and nylon are widely used, along with metals, ceramics, and composite materials. Material choice depends on the mechanical requirements, environmental stability, appearance, and other product specifications. TPU and PU stand out for their durability, flexibility, and capacity to withstand repeated bending or compression. As we shall explore, both share similarities but differ in certain key aspects that inform suitable applications.
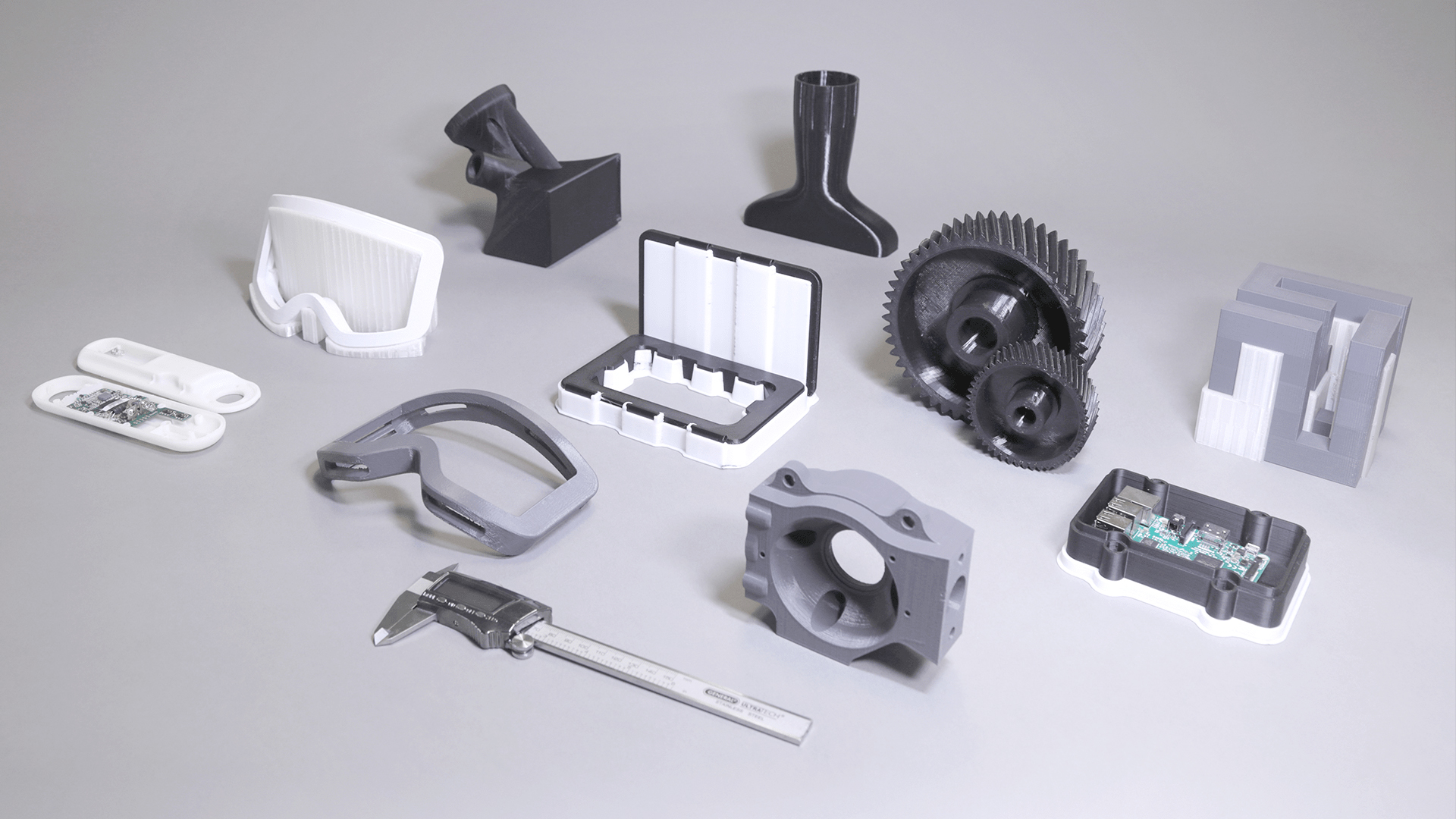
What is TPU?
Thermoplastic polyurethane (TPU) is a unique subclass within the family of elastomeric polymers, valued for high elasticity and durability similar to rubber but with the processing advantages of thermoplastics. Its molecular backbone contains long chains of alternating hard and soft segments, conferring both flexibility and mechanical strength. The hard segments act as connection points, with extensive hydrogen bonding cross-linking the polymer chains into an interconnected 3D network. This robust matrix enables TPU to repeatedly stretch and rebound to its original dimensions without permanent deformation, which is ideal for products designed to withstand squeezing, twisting, and bending motions. Common commercial applications capitalizing on these qualities include footwear components like shoe soles and midsoles, sporting goods ranging from ski goggles straps to the soft exterior of balls, medical tubing and devices, insulation foam around pipes or walls, rollers within conveyor systems, and flexible electronics needing to endure repeated flexing without failure. Within 3D printing, TPU’s abrasion resistance, flexibility, and ability to interface with support materials make it amenable to printing fully functional prototypes and end-use products with complex movable/bendable geometries.
What is PU?
Polyurethane (PU) refers to a broad class of polymers containing urethane groups as part of their molecular architecture. The versatility of PU chemistry facilitates diverse customization of mechanical performance across industrial and consumer sectors. PU can be formulated as either thermosetting or thermoplastic materials, with distinct implications:
Thermoset PU undergoes irreversible curing during manufacturing, permanently hardening through extensive cross-linking without the possibility of later melting or reshaping. Common applications taking advantage of hardness and thermal stability include insulation foam, abrasion-resistant coatings, durable sealants/caulking, structural adhesives, and rollerblade wheels designed for a smooth ride.
In contrast, thermoplastic PU softens upon heating and can transition repeatedly between solid and liquid states. This offers the advantages of easier processing, potential remixing of scrap material, and recycling at end-of-life. Thermoplastic PU applications ranging from furniture upholstery to foam mattresses to clothing like spandex and swimwear all benefit from the balance of flexibility, breathability, and protective cushioning it provides. Additional uses across the automotive sector include supple interior instrument panels and tough external car bumpers able to flex and rebound from minor impacts.
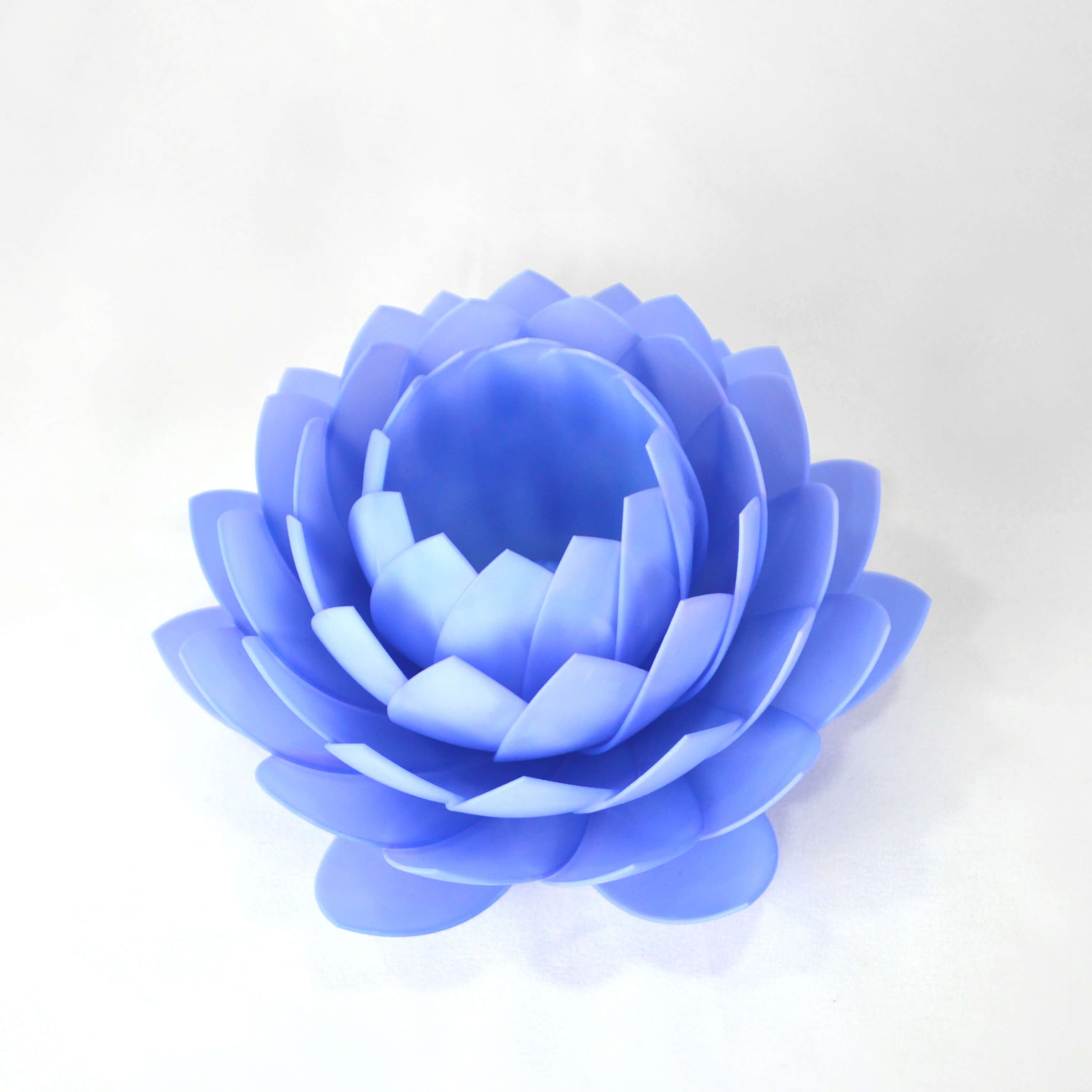
TPU in 3D Printing
As a thermoplastic, TPU is broadly compatible with common material extrusion 3D printing processes such as fused deposition modeling (FDM). In FDM, TPU filament wound onto spools is fed into a heated printer nozzle, melting within the temperature range of 205-230°C before being precisely deposited onto the print surface. Key parameters for high-quality FDM printing with TPU include:
- Print temperatures are set between 220-250°C to facilitate adequate flow and bonding. At lower temperatures, the viscosity of molten TPU remains too elevated for smooth extrusion.
- Heated print bed temperature of 50-60°C to mitigate part warping effects stemming from uneven cooling and contraction of the printed layers.
- Slower print speeds range from 30-50 mm/s in comparison to more rigid plastics. The relaxed speeds give recently deposited beads enough time to bond with the underlying layers before the next pass.
- Direct drive extruders with appropriately customized retraction settings help counter the stringing commonly associated with flexible filament printing.
Mastering the balance of TPU’s inherent flexibility against the need for neatly defined prints poses initial challenges for 3D printing beginners. However, with well-tuned parameters and extruder calibration, even novice users can achieve intricate TPU prints combining elasticity, strength, and precision.
PU in 3D Printing
While thermoplastic PU sees niche usage with material extrusion methods, thermoset PU more commonly serves roles as photopolymer resin formulas in vat polymerization 3D printing processes. Here, a liquid PU resin bath is selectively cured and solidified when exposed to a scanning light source, typically UV or visible wavelengths. Controlled light activation builds the 3D object from the vat bottom up. Polyurethane resins enable remarkably smooth printing of products with high elasticity, tear resistance, and durability. Resolution capabilities also excel relative to extrusion techniques. Biocompatible grades are popular for medical devices and implants. With superb chemical tolerance, polyurethane resins also suit applications involving solvents, fuels, lubricans, and paints.
However, uncured PU photopolymer resins require cautious handling, given irritation and toxicity risks before full solidification. They also commonly demand extended post-print UV curing to attain complete polymerization and optimal mechanical performance. Support structures may likewise prove difficult to remove after printing without damaging the product.
Comparative Analysis: TPU vs PU
When evaluating materials for 3D printing, how do TPU and PU compare regarding flexibility, strength, and printability?
- Flexibility: TPU reigns supreme in elasticity and resilience, easily compressing during deformation and then bouncing back instantly to regain its original dimensions without distortion. PU grades similarly allow compressibility yet lack the same shape memory, instead remaining permanently indented after pressure is applied.
- Tensile Strength: Photopolymer PU resins generally achieve higher tensile strength values in the range of 65-70 MPa, benefiting printed parts with enhanced rigidity. However, elongation at break suffers, rendering such PU quite brittle. In contrast, annealed TPU boasts elongations above 500% while approaching nylon-rivaling tensile strength exceeding 60 MPa, combining durability with flexibility.
- Ease of Printing: Cost-effective TPU filaments are widely accessible across consumer and industrial FDM 3D printers. However, printing consistent, high-quality TPU components requires meticulously dialed-in parameters and extruder calibration. PU photopolymers handle superbly across vat polymerization methods in terms of resolution, but uncured resin toxicity necessitates additional safety precautions during handling and cleanup.
- Range of Applications: Material selection closely aligns with suitable printing techniques and end-use requirements. TPU remains a premier choice for FDM printing of elastic and wear-resistant goods where flexibility is prioritized, from shoe soles to watch straps to phone cases. Precision casting of PU photopolymers aims to leverage high feature resolution paired with elasticity and solvent resistance, which is important for medical, dental, and industrial applications.
In summary, while TPU filament and PU photopolymer resin offer some overlapping advantages like elasticity and durability, their distinct material properties suit different 3D printing technologies and applications.
Conclusion
This guide has compared two versatile materials – TPU and PU – for consideration in 3D printing applications. Both provide exceptional flexibility and durability, with the distinction between TPU as a thermoplastic and PU’s thermoset or thermoplastic variants. Material choice interplays closely with suitable printing techniques and product specifications. As 3D printing advances continue broadening material capabilities, both TPU and PU will feature prominently thanks to their customizable mechanical properties balanced by ease of processing.
Read More
- 3D printing – Audio plastic shell
- Understanding the Vacuum Casting Process: A Comprehensive Guide | QSYrapid
- SLS vs FDM: A Comprehensive Guide | QSYrapid•https://www.qsyrapid.com
- `Ultimate Guide to Multi Jet Fusion 3D Printing Service | qsyrapid`
- Choosing Polymer 3D Printing: SLS vs SLA•https://www.qsyrapid.com